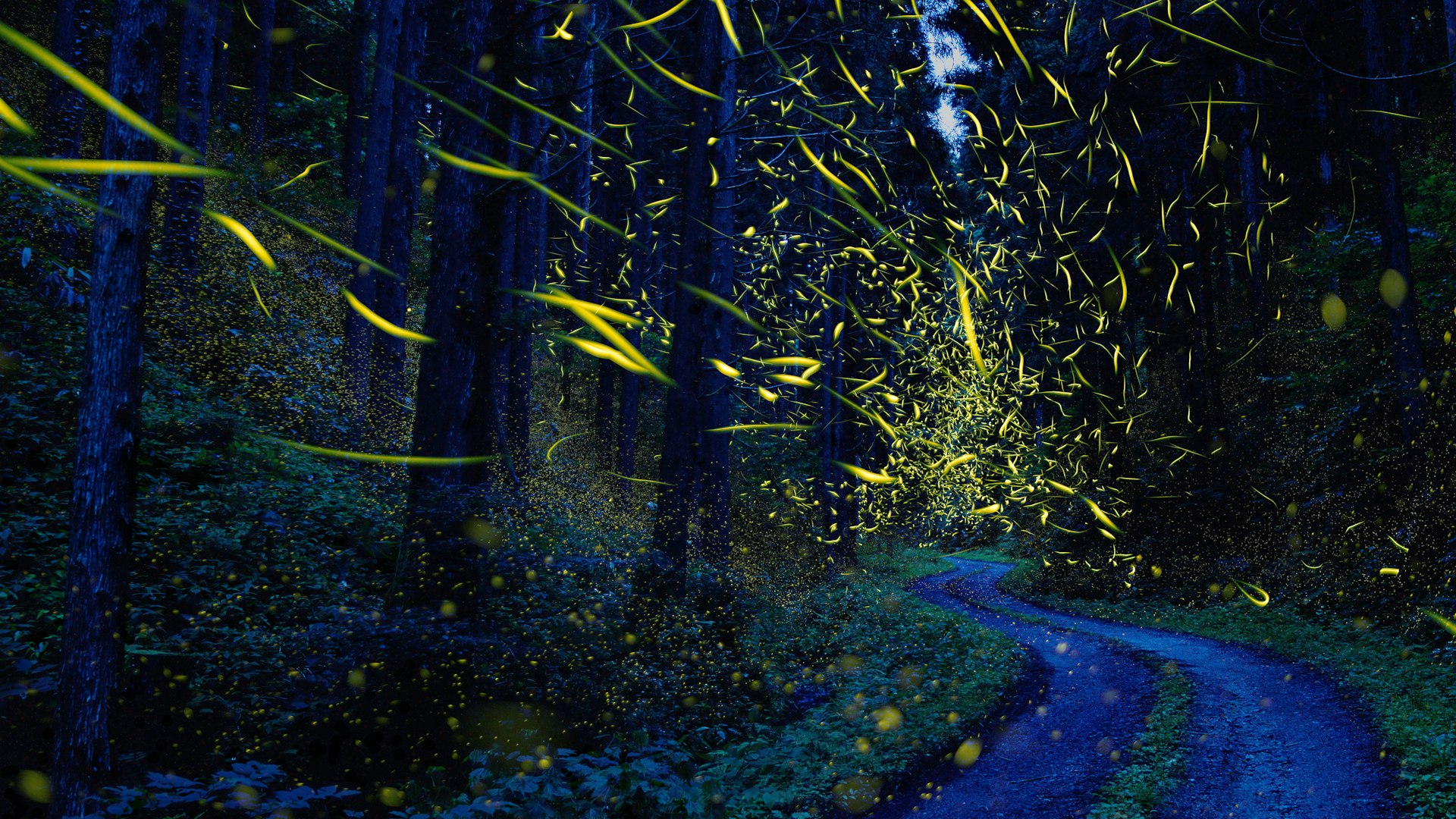
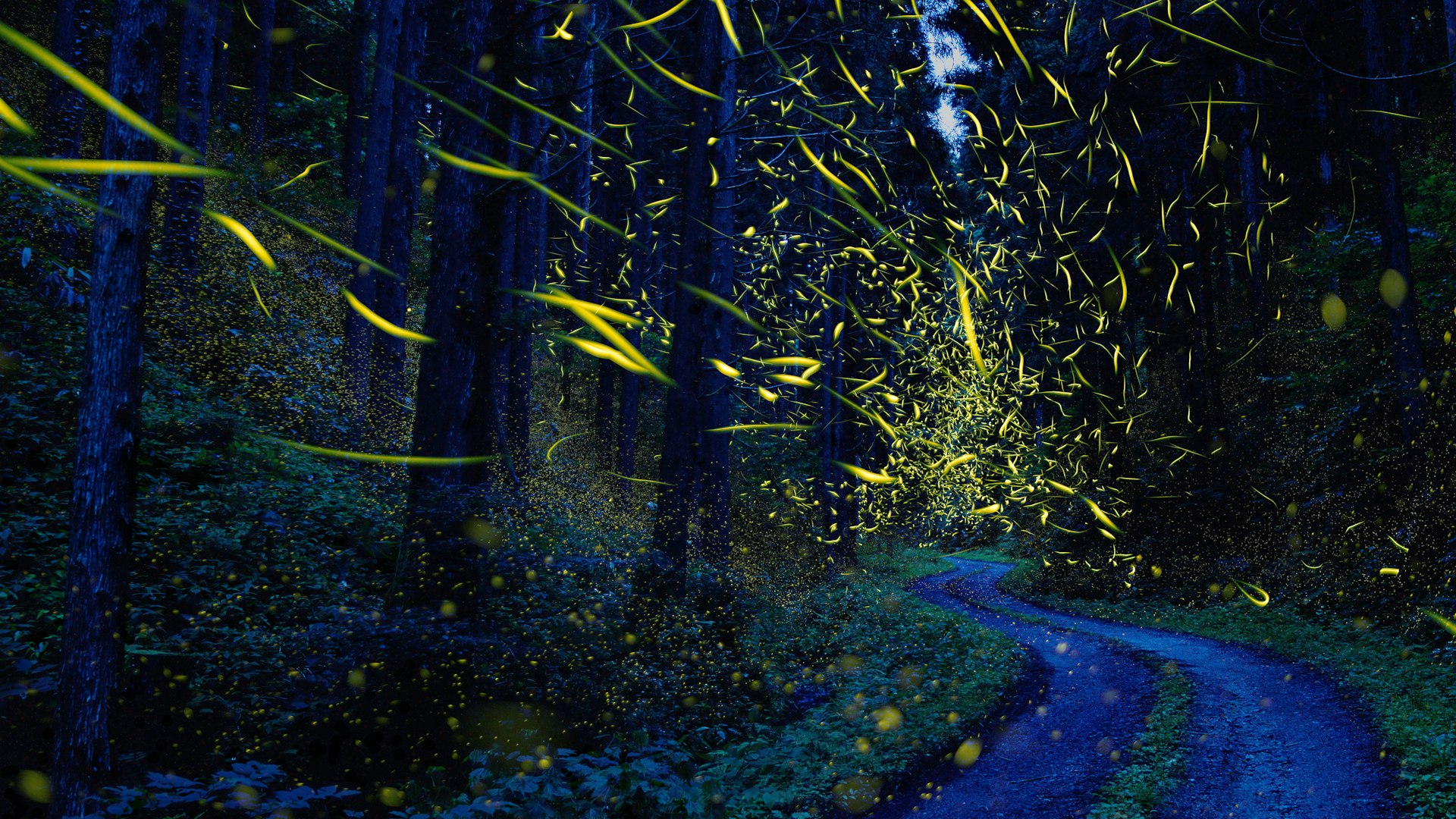
News and insights
Rankings, announcements, celebrations and other news from Henley Business School plus leading insights from our academics on current events .
Rankings, announcements, celebrations and other news from Henley Business School plus leading insights from our academics on current events .
This site uses cookies to improve your user experience. By using this site you agree to these cookies being set. You can read more about what cookies we use here. If you do not wish to accept cookies from this site please either disable cookies or refrain from using the site.